Why Switch to our Bags?
Supply chain issues? Breaking bags? Freezing problems? Our Aramus™ bags can get you back to making lifesaving therapeutics.
Aramus bags are the most versatile single-use solution available and can replace PE bags and bottles in a myriad of applications seamlessly. Swapping existing single-use bags with our Aramus fluid handling solutions is a smart way to keep your process moving when supply-chain issues occur, ensuring you can continue to deliver the cleanest, safest product without interruption. Compatible with hot, cold, and reduction of particulates in final process fluids, Aramus bags make sense and are easy to implement. With quick turnaround times, and customer-friendly compatibility, consider our comprehensive set of bag solutions to resolve your process challenges.
Easy to Fit into Your Process: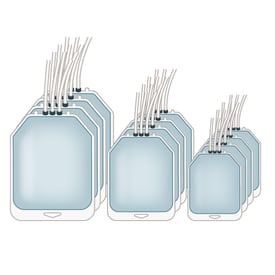
- Custom assembly lead times as short as 6-8 weeks thanks to our robust supply-chain infrastructure
- <7 mL to 20 L bags in stock along with assembly components
- Custom-configurations in a variety of sizes, including tubing and connectors to fit specific needs
- Achieve maximum sample retrieval
Quality You Can Count on: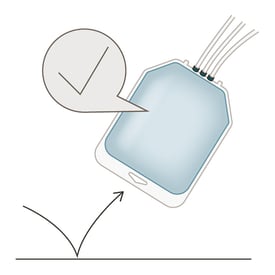
- Manufactured in an ISO Class 5 cleanroom, above the industry standard of Class 7, reduces particulate and contamination risk.
- Multiple manufacturing sites provides peace of mind
- Chemical compatibility with DMSO and many other chemistries
- Stays strong at extreme temperatures, -196° to 121°C (-321° to 250°F)
- Low extractable leachable (E&L) profile
- Animal origin free
- Built-in traceability (each bag is imprinted with identification number)
- Comprehensive validation package
Enables Customer Outcomes: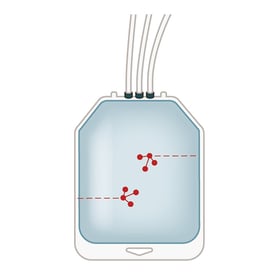
- Increased drug product yield in cold chain workflow–Aramus bags resist damage, reducing product loss
- Reduced out of specification (OOS) incidents, less time investigating unknown particulates–Aramus bags have lower particulates per volume versus other bags
- Reduced CAPA(s) due to unknown contaminants-Aramus defined E&L profile only has one arbitrary element
- Increased throughput/manufacturing efficiency in large scale freeze processes-Aramus bag footprint is optimized to container/freezer size
- Increased recovery with a lower surface energy– Aramus bags provides excellent recovery of product.
Access our Validation Guide to Learn More!