The automotive supply chain is transforming with the development of autonomous vehicles. The rise of electronic systems leads designers and manufacturers to seek collaboration partnerships.
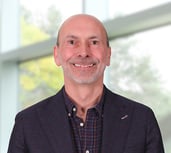
Antoine Amade, senior director EMEA/NA sales, was recently interviewed by SEMI to discuss the zero-defect challenges facing semiconductor fabs and the expansion of the GAAC (Global Automotive Advisory Council).
“Minimizing latent defects is now a top priority in semiconductor fabs. However, there is a gap between visible and non-visible defects. Although fabs can detect small defects, human intervention is still needed to manage them. We are witnessing a fundamental shift in the contamination control strategy in auto chip production, from contamination control for yield to contamination control for reliability”, said Amade.
Visit the SEMI blog to learn more about the GAAC, and to watch the full interview.
Visit our automotive reliability page to learn more about the New Collaborative Approach and our contaminant management solutions, www.entegris.com/automotive.