Phobic vs. Philic: How the Process Indicates the Membrane in Bioprocess Applications
Some membranes attract water, and some actively repel it. Those that attract water are known as “hydrophilic,” and those that repel water are known as “hydrophobic.” Which kind of membrane is best suited for your application?
Hydrophilic Membranes are Paired with Liquid Applications – Most of the Time
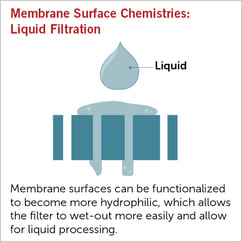
In hydrophilic membranes, the surface tension of water is lower than the surface energy of the membrane. In hydrophobic membranes, the reverse is true – the surface tension of water is much higher than the membrane's surface energy. For more details, watch Dr. Aiwen Wu, Applications Engineering Manager, demonstrate the wetting properties of various membranes.
If you’re performing a typical bioprocess liquid application, such as making cell culture media and buffers, then you’ll probably prefer to use a hydrophilic membrane. That’s because most biological processes rely on water as a natural medium.
On the other hand, if you’re working with an application such as cell culture or freeze/thaw, because of the processes and materials involved, hydrophilic membranes may not be the best choice.
First Consider the Application, Then Consider Material Compatibility
Freeze/thaw applications often involve harsh chemicals such as dimethylsulfoxide (DMSO). Meanwhile, most hydrophilic membranes are made from PES or PVDF . These membranes aren’t compatible with DMSO, because contact with DMSO may cause them to corrode. Check out our compatibility page for more information on which membranes mix well with which chemicals.
On the other hand, PTFE membranes have much broader chemical compatibility than PES or PVDF, and they can resist high heat and corrosion. But PTFE is hydrophobic – how can you use it in liquid applications?
Prewetting Unlocks Hydrophobic Membranes for Liquid Applications
Hydrophobic membranes can be utilized in liquid applications when there is no other option, but they must be prewet. That’s because prewetting floods the membrane with a liquid that has low surface tension, allowing other fluids to pass through more easily.
Prewetting makes hydrophobic filters viable in liquid applications, but there are a few caveats:
- In traditional single-use applications, the membrane only needs to be wet out once and then disposed of. If the filter is reused or allowed to dry out, it should be rewetted after sterilization.
- End-users usually need to wet the filter out manually. If you’re trying to scale from lab to commercial volumes, however, it may be worth looking into automated processes that can save time.
- If you need to wet out a filter with a solution that has a lower concentration of alcohol, you may need to apply the solution at a higher pressure in order to fully saturate the material.
Essentially, prewetting is the only way to successfully use a hydrophobic membrane in a liquid application. But where do hydrophobic membranes truly excel?
What’s the Best Use-Case for Hydrophobic Membranes?
Hydrophobic membranes excel during gas filtration processes. The low surface tension of a hydrophobic membrane repels water — but unlike water, air is non-polar and can pass efficiently through a hydrophobic membrane. In short, hydrophobic filters let gas through while barring liquids. Why is this important?
The benefit of a hydrophobic membrane is that it makes separating gas and liquids very easy while also providing a sterile barrier. Applications such as bioreactors, fermenters, rocker bags, and culture media all produce gases that must be purged. Some liquid applications will also use air or nitrogen to move fluid through a system. Hydrophobic filters will let gases move out of these systems without letting them back in. Because they’re sterile, it’s safe for fluids to come into contact with them.
Troubleshooting a Hydrophobic Membrane
Pressure – specifically over-pressurization – is among the biggest concerns when implementing hydrophobic membranes for gas filtration. For example, at a high enough pressure, liquid from the application can overcome the surface energy of the membrane and be forced into the filter. This causes blockages, which can reduce flow rates and disrupt performance. It can also entail a certain amount of product loss.
Over-pressurization can be caused by an operator error, such as someone closing the wrong valve. More subtly, operators may fail to account for the excess gas volume produced by cells within systems such as bioreactors. This can also over-pressurize the system and lead to blockages.
Condensation is a different concern. This is caused by temperature differentials between the inside and the outside of a system. Because the gas filter is the interface between the inside and the outside of a system, it’s exposed to high temperatures on one side and lower temperatures on the other. This means that liquid from the air outside the system can condense inside the filter and block it.
The best way to avoid this is by putting a heater jacket around the filter to eliminate the temperature differential. This will prevent water from condensing and preserve the efficiency of your hydrophobic filter.
Make Sure to Choose the Correct Filter Membrane for Your Application
Remember that choosing the right filter material is a high-stakes decision. Opting for the wrong membrane material may affect the integrity of your production process and lead to lost batches of expensive products and precursors. You’ll also lose time diagnosing and fixing the error. Download our life sciences filtration ebook to learn how our product portfolio, combined with our expert knowledge, can guide you to success.