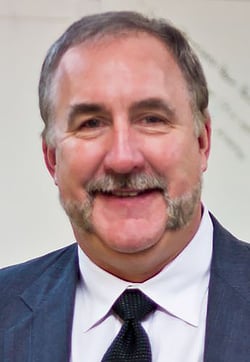
As the chief technologist for the Life Sciences Division at Trane Technologies, Scott Farrar knows a thing or two about ultra-low temperature control for the life sciences industry, perhaps drawing inspiration from his days at Penn State University enjoying peach ice cream. Scott’s biggest inspiration, however, was his entrepreneurial dad who started a solar equipment company, teaching Scott from a young age the importance of sciences, technology, engineering, and mathematics (STEM) education and solving problems. Scott carried those tools with him, and upon completing his formal education, went to work for a pharmaceutical manufacturing company in research and development, specializing in low-temp freezers and incubators as well as heat-momentum and mass-transfer-type processes for the pharmaceutical industry. His exposure to dilemmas and investigative approach is what drove him to create better customer experiences.
A natural problem-solver and entrepreneur, Scott started Farrar Scientific, now known as FARRAR™ in 1996. Scott grew FARRAR from consulting to its current position as a leader in ultra-low temperate control, filling unmet needs for flexible, modular, and efficient ultra-low temperate process and storage, including cooling and heating/thawing. Now, with FARRAR, a brand of Trane Technologies, he has his ideal job “finding problems, setting them up, and knocking them down.” Guided by his pulse on the life sciences industry and decades of experience, Scott sees a considerable opportunity to improve processes within biopharma storage and is coming up with something significantly better than what’s available on the market today.
When it comes to working with customers, FARRAR starts by focusing on customer need. This solutions-oriented experience provides customers with insight specifically for their process. A new BioSolutions Center in Davidson, North Carolina gives customers the opportunity to see FARRAR offerings in person.
Currently, FARRAR freezer chambers offer a unique forced air convection system ‘cyclone’ effect. A complete agnostic system, these chambers allow for storage of any sized product in an easy-to-control, accurate, mobile package. Offering the widest operating range of any freezer from +40˚ to -80˚C (+104° to -112°F), the freezer is programmable, dialing itself in precisely to the end-user’s requirements.
This technology has led to an exciting collaboration for FARRAR: integration with Entegris. Our two-dimensional and three-dimensional bags continue to solve complex biopharma problems, minimizing bag breakage and cryo-concentration, while complementing FARRAR freezer offerings.
An alternative to large-scale freezer farms or capital-intensive cold rooms used in the manufacturing of drugs, vaccines, and other biological products, FARRAR’s 4000 Series Controlled Rate Chambers greatly reduces freeze/thaw times from days or weeks to hours, optimizing manufacturing efficiency and improving characteristics such as uniformity and repeatability versus competing technologies.
The company has come a long way since that first inspirational taste of ice cream. ‘The luckiest guy on earth’ has helped build the right tool for the right application for customers, and loves going to work each day to solve problems whether through a piece of equipment or a process improvement. Together, FARRAR and Entegris are stronger, and the customer wins with end-to-end solutions.
Read more about our collaboration.